摘要: 計量儀表在企業生產經營優化、計量結算等方面發揮至關重要的作用。借助 RS485 總線技術實現計量儀表數據采集是企業實現信息化、智能化的根本保障。文章通過對現有數采系統通訊存在的問題,進行了深入分析,優化調整現有總線和通訊采集結構,確保了系統穩定可靠傳輸,提升了儀表運行監測水平,為生產經營提供了及時準確計量數據。
目前大部分計量儀表都具備 RS485 通訊接口,同時 RS485 總線技術因具有可靠性高,結構簡單,速度快等優點,被廣泛應用于計量儀表數據采集與監控系統中。目前天津分公司具有貿易交接及部際互供各種能源物料計量儀表 342 條回路,介質涵蓋原油、天然氣、成品油、水、電、汽、風 等 40 種。各種計量儀表都通過應用 RS485 總線技術組成能源物料數據采集監控系統,自投入運行
以來,在企業計量結算、生產經營優化、降本減費方面發揮了重大作用。
1 現狀及問題
1. 1 現狀
為實現企業計量儀表信息化管理,早在 2003年筆者公司就基于 RS485 總線技術,應用 IFix 組態軟件建立起計量儀表數據采集 SCADA 系統,目前儀表采集點數 3 300 余點。公司每年管輸能源物料如天然氣 ( 3. 42 億 Nm3 ) 、原油( 1 202 萬 t) 、成品油 ( 170. 96 萬 t) 、新鮮水 ( 1 011. 38 萬 t) 、蒸汽 ( 1 033. 06 萬 t) 、氮氧氣 ( 2. 35 億 Nm3 ) 的計量結算都依靠該 SCADA 系統采集的基礎數據,同時為公司級管理系統如實時數據庫、計量管理信息系統、MES 等提供數據支撐。該系統的網絡結構如圖 1 所示。

1. 2 存在問題
隨著企業規模的不斷擴大,系統接入的采集儀表數量、種類不斷增多,近幾年在數據通訊傳輸方面出現了一些問題,給計量監控及結算帶來不小的困擾,主要有如下表現。
( 1) 計量儀表通訊響應速率降低,延遲較大,部分儀表返回數據在 1 min 甚至更長時間。
( 2) 一些站點數據采集出現時斷時續情況。
( 3) 公司生產部門 MES 系統班報要求在計量人員在 30 min 內完成 342 臺儀表數據報送,經常出現采集中斷,人員手工應急錄入導致超時提報,容易受考核,給班組人員帶來不小壓力。
( 4) 頻繁數據中斷,給計量運行狀態監控、計量結算帶來極大影響,容易出現計量糾紛。
2 原因分析
為徹底解決采集系統通訊存在的問題,確保數據傳輸穩定可靠,我們從 RS485 通訊總線結構、計量儀表通訊協議 ( Modbus RTU) 、IFix 軟件通訊組態等各項內容進行了分析排查。
2. 1 RS485 總線
RS485 采用半雙工工作方式,支持多點數據通信。RS485 采用平衡發送和差分接收方式實現通信,#大的通信距離約為 1 219 m,#大傳輸速率為 10 Mb /s,傳輸速率與傳輸距離成反比,在 10 kb /s 的傳輸速率下,才可以達到#大的通信距離,如果需傳輸更長的距離,需要加 485 中繼器。 RS485 總線網絡拓撲一般采用終端匹配的總線型結構。即采用一條總線將各個節點串接起來,不支持環形或星型網絡。RS485 總線一般#大支持 32個節點。
系統建設初期由于缺少 RS485 總線結構整體規劃,為了實施方便采用了錯誤的組網方式,雖然該方式在儀表數量不多,數據訪問量不大時也能通訊,但為后期儀表數量增多時埋下隱患,嚴重影響通訊速率。錯誤的總線連接方式如圖 2 所示。
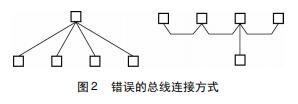
2. 2 Modubs 通訊協議
Modbus 是一種串行通信協議,已經成為工業領域通信協議的業界標準,目前大多數計量儀表都具有 RS485 通訊接口,支持 Modbus 通訊協議。 Modbus 協議采用 master/slave 架構。有一個節點是master 節點,其他使用 Modbus 協議參與通信的節
點是 slave 節點。每一個 slave 設備都有一個非常好的地址。
目前中心管理的 342 臺計量儀表按結構可分為 ( 質 量、渦 街、電 磁、差 壓、超 聲、容 積 式、流量積算儀) 7 類 20 余個廠家不同型號的產品。這些產品都標明完全遵循標準 Modbus RTU 協議。但當現場總線接在一起進行組網通訊時,出現了問題,為此我們開展了測試。
測試結果表明: 進口質量流量計通訊性能兼容性較好,部分國產計量儀表協議標準不規范,同一回路連接超過 3 種類型 10 臺以上儀表通訊會出現收發超時,數據解析異常等情況,其中中斷嚴重的煉油站儀表超時率 1. 22‰ ( 允差 0. 5‰) 、重試率 0. 85‰ ( 允差 0. 5‰) 、錯誤率 54. 8‰ ( 允 差 1‰) 、超載率 11. 1‰ ( 允差 1‰) ,整體通訊速率低。
2. 3 IFix 通訊組態配置
IFix 軟件組態配置方法流程如圖 3 所示。

對儀表通訊速率有重要影響的配置在于1和2兩步本次針對步驟1中的 I/O 驅動配置進行查驗。中心數采系統應用 IFix 的 I/O 驅動為 MB1 ( 7. x 版 本) 定義串口端口號、主站地址、響應超時、重試、延遲時間。
經過現場檢查各站配置,在驅動器中增加儀表且不同儀表配置在同一 COM 口時,系統驅動器MB1 的 配 置 選 項: 主 輪 詢 速 率 ( Primary Poll Rate) 、響應超時都采用了默認配置的 1 秒,這樣在通道儀表過且存在通訊協議兼容性差的情況下會出現在儀表還未來及響應時上位機重復發送讀取數據的情況,從而出現通訊延時。同時在組態時將儀表流量、溫度、壓力、累計等各寄存器地址分開塊組態的情況,在上述多參數讀取時上位機需要單好發送每條讀取指令,效率嚴重降低。
3 總線及采集結構優化
3. 1 RS485 總線優化調整
( 1) RS485 布線不可以布置成星型接線與樹形接線。RS485 布線規范是必須手牽手的布線,如直接布設成星型連接和樹形連接,很容易造成信號反射導致總線不穩定。很多施工方不規范布線,在儀表數量不斷增多時,采集通訊出現了問題。針對 RS485 總線組網方式錯誤的問題,將現場或盤柜內每條 RS485 回路儀表連接方式按照標準菊花鏈 ( daisy-chained) 方式連接在一起,如圖4 所示。
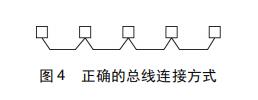
( 2) 在每臺處于總線末端的儀表通訊端口都增設了 250Ω 電阻,以此消除環境溫度變化有可能對總線回路電阻帶來的影響。
3. 2 通訊協議標準化改造
( 1) Modbus RTU 協議轉換為標準 Modbus TCP協議。根據分析及現場測試得出的部分儀表 Modb- us RTU 協議不標準以及兼容性差,我們應用 MOX- A 公司 NPORT5630 串口服務器替換原來的研華多串口辦卡 CP-118EL,實現非標準協議到標準協議轉換,轉換為 Modbus TCP 協議后同時也解決了多臺上位機同時采集一臺儀表數據問題。
( 2) 將現場不同廠商儀表進行分類,同一類型的分配至串口服務器的同一 COM 口進行采集。能夠規避協議兼容性影響的同時,由于該串口服務器都具有多個 COM 口,為以后系統擴充升級打下了基礎。
3. 3 IFix 通驅動標準化改造
( 1) 將上位機 iFix 采集軟件中驅動程序由原來的 MB1 驅動 ( Modbus RTU 協議) 變更為 MBE驅動 ( Modbus Ethernet TCP 協議) ,以完成協議標準化轉換。
( 2) 修改驅動器中儀表參數寄存器地址讀取方式。由流量、溫度、壓力、密度、累計分別讀取的方式改為配置成一個包一次讀取。
( 3) 對 MBE 驅動器中每臺儀表主輪詢時間、響應超時、等待時間、重試次數等關鍵通訊參數進行優化調整。如適當降低主輪詢時間 ( 1 s 變為5 s) ,以避免頻繁發送讀取數據而儀表不能及時響應造成的信息獲取超時、擁堵、識別錯誤等故障發生。此處需結合現場通道連接儀表數量做出相應設置,為經驗值,無法統一固定。
4 優化效果
( 1) 通過應用 iFix 軟件任務管理對各采集站驅動通訊收發情況進行監視,各通道通訊狀態良好,通訊超時率降為 0. 27‰,重試率 0. 3‰,超載率為 0,全部在允差指標范圍內。可以看出通訊效果得到明顯改善。
( 2) 通過優化及調整,我們對目前各采集站儀表通訊響應速度進行統計,原采集各站儀表平均通訊響應速度為 48 s,優化調整后為 21 s,響應速度提高了2. 3 倍,同時極大的提高了系統運行穩定性。
( 3) 計量儀表數據的穩定采集不僅關系到石化企業正常生產運行監控,同時精準、快速的數據采集關系到企業經濟效益、貿易結算。據統計石化企業正常生產主要物料投入產出合計流量約 5 000 t /h ( 其中物料 2 800 t /h,能源 2 200 t /h) ,1秒平均值在 1. 39 t。通過此次系統結構優化調整,提高了采集速度和系統運行穩定性,同時通過應用系統加強監控,及時發現計量儀表、工藝等異常狀態,每年為公司找補回原油、航煤、天然氣、石腦油等各種能源物料損失 900 噸,避免直接經濟效益損失約 400 萬元。
5 總結
計量儀表作為石化企業生產經營優化、效益監測的千里眼,其數據的穩定采集可靠傳輸是企業實現信息化、智能化的根本保障。本文通過對企業能源物料計量儀表數據采集通訊網絡現狀問題開展詳細分析,優化調整 RS485 通訊總線及采集結構,解決計量儀表信號傳輸不穩定問題,提升了計量儀表運行監測水平,為生產經營提供及時準確計量結算數據等方面充分發揮計量把關作用,效果顯著。同時對于同行業計量儀表數據采集通訊方面可起到參考借鑒意義。